What Happens If You Choose the Wrong Filter Cloth?
Lug 18, 2025
In the world of industrial filtration, few components are as deceptively simple yet critically important as the filter cloth. At first glance, it may appear to be just another layer in a membrane filter press or belt filter press, but its role in solid-liquid separation cannot be overstated. The wrong filter cloth can quietly compromise your entire process, reducing efficiency, shortening equipment lifespan, and inflating operating costs.
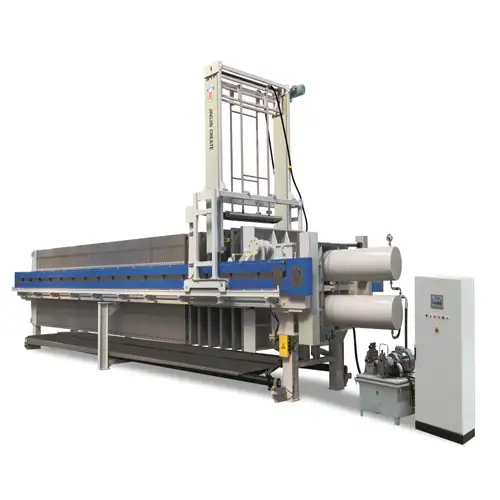
Why Filter Cloth Selection Is a Strategic Decision
The filter cloth acts as the frontline barrier in separating solids from liquids. Its weave structure, material type, and finish all determine how effectively it can retain particles, release cake, and withstand harsh operating conditions. In a membrane filter press, where pressure cycles are intense and cake dryness is critical, a poorly matched filter cloth may not only reduce output quality but also cause physical damage to the membrane plates. This results in unexpected downtime and costly replacements—both of the cloth and, eventually, the press components themselves.
On the other hand, in a belt filter press, where the cloth moves continuously under tension, the wrong material can stretch, misalign, or degrade prematurely. Poor drainage can lead to soggy, low-solids cake, while inconsistent porosity may create bottlenecks in throughput. Even when a unit has a competitive belt filter press price, the wrong cloth choice can negate that value by increasing long-term maintenance and reducing productivity.
Operational Consequences of the Wrong Filter Cloth
Filter slurry does not correspond with the characteristics of the filter cloth or the equipment used; vulnerability to performance issues arises in rapid succession. In case the slurry is composed of abrasive particles, it may cut away the fabric if it’s of soft nature. The same can happen in the presence of a chemical such as polyester or nylon, if the cloth isn’t properly coated. Furthermore, the insufficient porosity becomes a factor causing an increase in backpressure, and excessive openness is equal to allowing the penetration of dirt; hence, the filtrate becomes contaminated and non-compliant with the rules.
The third case that can be easily seen is the lack of transparency of the cake. If the cloth is too tightly stuck to the cake, it becomes hard to use and requires manual removal after a few cycles. In the case of a high-volume industrial environment, this single inefficiency can become even more apparent where the cloth needs frequent washing and the replacement is at a premature stage.
The Link Between Filter Cloth and Long-Term Cost
A common misconception is that filter cloth is a minor cost component that doesn’t need strategic evaluation. In reality, it’s a performance lever that directly influences the lifespan of the press, the clarity of the filtrate, and the consistency of the throughput. Choosing the correct filter cloth not only improves productivity but also reduces wear on other components—like gaskets, plates, and bearings—especially in high-pressure systems like a membrane filter press.
Additionally, downtime due to cloth-related issues is rarely limited to the cloth alone. Operations are halted, schedules delayed, and entire workflows disrupted—sometimes for hours or days. While the belt filter press price may be attractive upfront, using the wrong cloth can chip away at margins by introducing inefficiencies and hidden costs over time.
Best Practices for Smart Filter Cloth Selection
To avoid these pitfalls, operators should take a holistic approach. Understand the slurry composition—whether it’s acidic, alkaline, abrasive, or oily—and select materials accordingly. Evaluate temperature, pressure cycles, and mechanical load. Consider cake characteristics: will it be dry and brittle, or sticky and elastic? The right filter cloth balances filtration rate with retention and clean release.
Why JingJin Filter Offers an Edge
At JingJin Filter, we recognize that no two filtration processes are the same. By this understanding, we not only deliver top-performance membrane filter presses and belt filter presses but also assist in the selection of the most suitable filter cloth according to narrowed process requirements. Our accomplished engineers cooperate with customers to complete the slurry samples’ tests, to find the weave types, and to adjust the system in progress. We will also be proposing up-to-date solutions for you to meet the opportunities that are likely to be energy-saving, taking less space, cost-efficient, producing economic benefits, reducing financial load, and eco-friendly during the whole life cycle (Cleantech).
Selecting the correct filter cloth is not simply an execution of the buying process but rather a strategic move that ensures your plant stays up, attains efficiency, and keeps high performance.