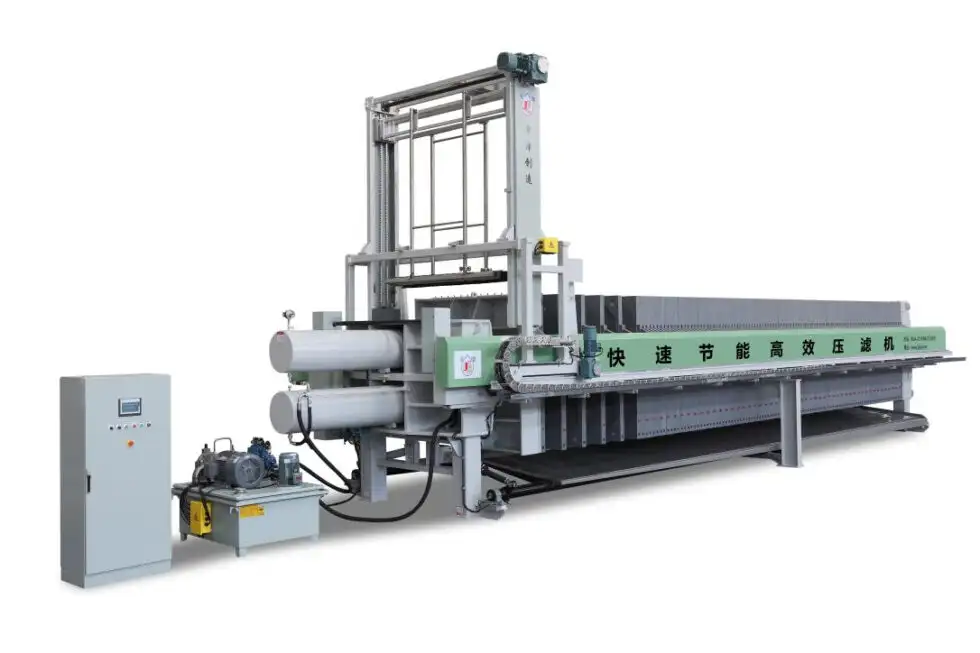
Membrane Filter Press
1.High-Quality Materials
2.Advanced Technology
3.Various Filter Plate Options
4.Automatic Operation
5.Membrane Squeeze
6.Large Capacity
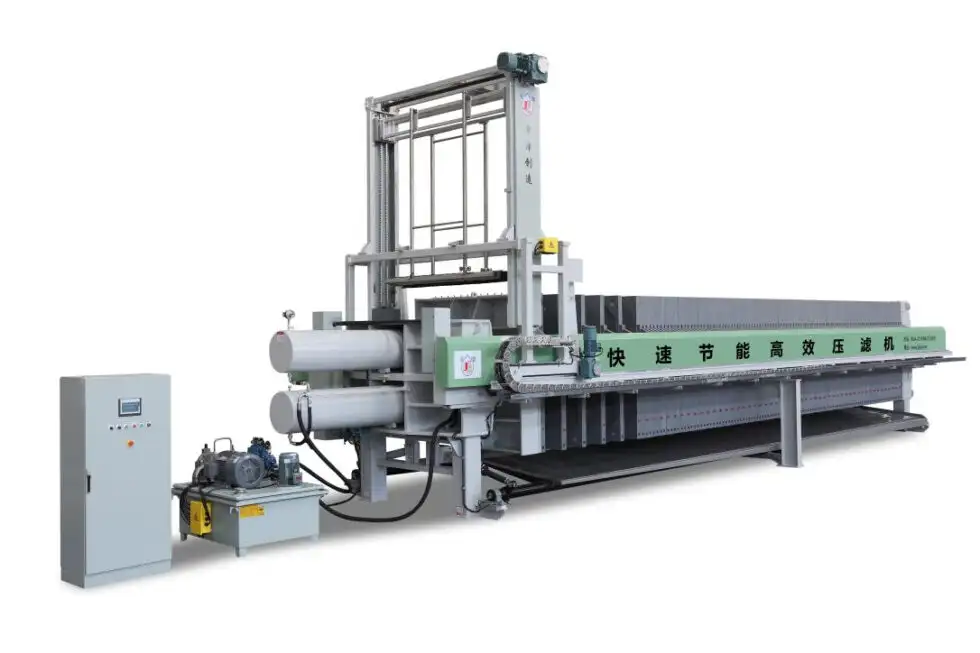
Membrane Filter Press-used in various industries
A membrane filter press is a sophisticated type of filter press widely used across numerous industries for efficient solid-liquid separation. This advanced variation of the traditional filter press incorporates a flexible or elastic membrane within the filter chamber, which can be made from materials such as rubber or elastomers.
Membrane filter presses are employed in diverse sectors, including wastewater treatment, chemical processing, mining, pharmaceuticals, and food and beverage, among others. They are particularly valued for their ability to achieve high efficiency and reduce environmental impact, significantly enhancing the overall productivity of industrial operations.
Why choose Membrane Filter Press
1.Shorten the filtration cycle: Compared with traditional chamber filter presses, membrane filter presses can reduce the filtration cycle time by more than 50% on average, which directly improves production efficiency and capacity.
2.Reduce energy consumption: Due to the shortened filtration cycle and the increased degree of automation, membrane filter presses can save energy consumption during operation.
3.Improve safety: Modern membrane filter presses use the latest safety technology to ensure the safety of the operation process.
4.Reduce pump wear: Due to the lower feed pressure, the diaphragm filter press can reduce the wear of the pump when conveying abrasive media.
5.Flexible configuration options: The diaphragm filter press can be modularly designed according to different industrial and municipal needs, providing a variety of expansion modules and automation options.
How Does a Membrane Filter Press Work?
1.Charging the Filter Chamber: The process begins by filling the filter chamber with the slurry to be filtered.
2.Initial Filtration: The initial phase involves separating solids from liquids as the slurry passes through the filter media.
3.Membrane Inflation: The membrane is then inflated, applying additional pressure to the filter cake.
4.Enhanced Dewatering: This inflation stage enhances dewatering by squeezing out more liquid from the filter cake.
5.Final Filtration: Any remaining liquid is expelled, ensuring maximum dryness of the filter cake.
6.Cake Discharge: The dry filter cake is discharged from the press, ready for disposal or further processing.
Key Advantages of Membrane Filter Presses
1.Higher Filtration Efficiency: Membrane filter presses achieve superior cake dryness compared to traditional filter presses, significantly reducing the volume of liquid waste.
2.Shorter Cycle Times: The membrane squeezing stage accelerates the filtration process, resulting in faster cycle times and increased productivity.
3.Improved Cake Quality: The membrane aids in producing a more uniform and consistent filter cake, which is easier to handle and dispose of.
4.Reduced Environmental Impact: By generating drier filter cakes and minimizing liquid waste, membrane filter presses help reduce the environmental footprint of filtration processes.
If you are interested in our products, please contact us !